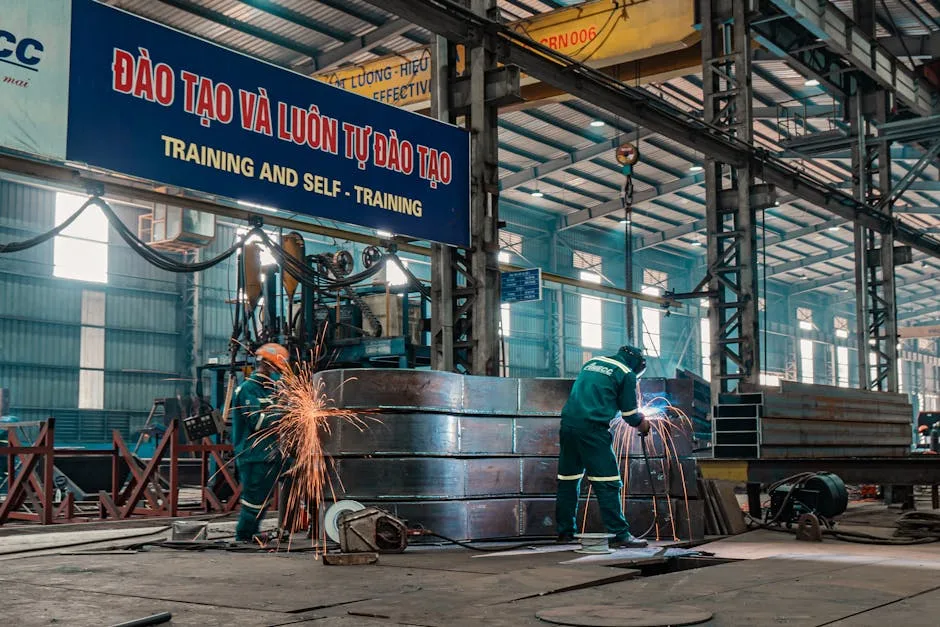
Mitsubishi Electric has begun implementing AI-powered translation software in its factories to address Japan’s growing labor shortage. The initiative aims to facilitate the hiring of foreign workers by removing language barriers in industrial settings. This move reflects broader trends in manufacturing automation and AI adoption, as companies seek solutions to workforce challenges.
AI Translation in Industrial Environments
The new system, developed under Mitsubishi’s Maisart AI brand, provides real-time translation between Japanese and multiple languages used by foreign workers. According to company statements, the technology integrates with existing manufacturing equipment and quality control systems. This allows non-Japanese speaking employees to operate machinery and follow safety protocols without language barriers.
Industrial applications present unique challenges for translation systems, including technical terminology, background noise, and safety-critical communications. Mitsubishi’s solution reportedly achieves 95% accuracy for factory-specific vocabulary, compared to 85% for general-purpose translation tools. The system also includes visual indicators and confirmation prompts to prevent misunderstandings in critical operations.
Broader Context of Manufacturing Automation
Mitsubishi’s translation initiative coincides with wider automation efforts across the manufacturing sector. A recent case study from Nordspan Automation demonstrated how a 25-employee manufacturer automated a Mitsubishi wire EDM machine, achieving 24/7 production and doubling machine utilization. The project showed return on investment in less than one year.
Other industrial firms are pursuing different AI strategies. Siemens has developed a generative AI copilot designed to optimize production processes for small and medium enterprises. These tools help compensate for workforce shortages while maintaining production quality and efficiency.
Workforce Challenges in Technical Fields
The labor shortage extends beyond manufacturing floor positions. A VDE report highlights that 63% of students drop out of electrical engineering programs in Germany, with women comprising only 9.8% of the workforce. Similar patterns exist in Japan, where aging demographics exacerbate skills gaps.
AI solutions like Mitsubishi’s translation system represent one approach to expanding the available talent pool. However, they don’t address the root causes of workforce shortages in technical fields. Education reform and improved retention strategies remain critical for long-term solutions.
Security Considerations for Industrial AI
Implementing AI systems in manufacturing environments introduces new security considerations. Translation systems connected to operational technology networks could potentially serve as attack vectors if not properly secured. Best practices include:
- Network segmentation between translation systems and critical control networks
- Regular security updates for AI model inference engines
- Access controls limiting who can modify or update translation databases
- Monitoring for anomalous translation outputs that might indicate system compromise
These measures help maintain both operational security and translation accuracy in industrial settings. As AI becomes more prevalent in manufacturing, security integration will remain a key consideration.
Future Implications
Mitsubishi’s translation system could set a precedent for other manufacturers facing similar workforce challenges. The technology may expand to include additional languages and integrate with augmented reality interfaces for maintenance tasks. However, successful implementation requires balancing automation with human oversight, particularly for safety-critical operations.
As noted in a recent EU chip strategy critique, technological solutions alone cannot resolve all supply chain and workforce challenges. Comprehensive approaches combining AI tools, education initiatives, and policy changes will likely prove most effective in addressing manufacturing sector shortages.
References
- “Mitsubishi Electric launcht eigene Marke für künstliche Intelligenz,” Industr.com, 2017. [Online]. Available: https://www.industr.com/de/mitsubishi-electric-launcht-eigene-marke-fuer-kuenstliche-intelligenz-2304823
- “Arbeitsaufwand erheblich reduzieren,” GO>>ing Magazine. [Online]. Available: https://www.go-ing.net/antreiben/arbeitsaufwand-erheblich-reduzieren
- Software4Production GmbH, “Mitsubishi Nordspan JBS Case Study,” LinkedIn, 2024. [Online]. Available: https://de.linkedin.com/posts/software4production-gmbh_mitsubishi-nordspan-jbs-activity-7246826012162838528-SiYN
- “KTM Insolvenz: Kapital und Teile fehlen – schon wieder Produktionsstopp bei KTM,” MSN Auto, 2025. [Online]. Available: https://www.msn.com/de-de/auto/nachrichten/ktm-insolvenz-kapital-und-teile-fehlen-schon-wieder-produktionsstopp-bei-ktm/ar-AA1DBJhV
- “Große Sorgen um Standorte von Chemiekonzern Dow,” MSN Finance, 2025. [Online]. Available: https://www.msn.com/de-de/finanzen/top-stories/gro%C3%9Fe-sorgen-um-standorte-von-chemiekonzern-dow/ar-AA1DBE5H
- “Studie: Deutschland hat auch Sachen KI-Fachkräftemangel,” Logistik Heute, 2024. [Online]. Available: https://logistik-heute.de/news/studie-deutschland-hat-auch-sachen-ki-fachkraeftemangel-188562.html
- VDE, “Arbeitsmarkt Studie 2022,” 2022. [Online]. Available: https://shop.vde.com/de/arbeitsmarkt-studie-2022
- AquaVentus Initiative. [Online]. Available: https://www.aquaventus.de
- VDE FNN. [Online]. Available: https://www.vde.com/de/fnn/arbeitsgebiete